UV CURING AND INERTING
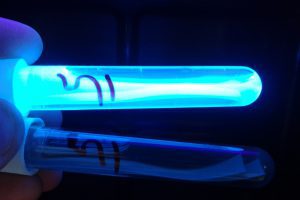
of low refractive index UV-cured polymers:
How to get good curing? How to get good inerting?
Inert Atmosphere Guide
The UV curing of acrylate monomers is a free radical polymerization process in which UV radiation is absorbed and activates a certain type of molecules, photoinitiators. The activated photo initiators normally break into reactive species called “free radicals” that start the polymerization of the acrylate groups. The free radicals are also very reactive towards molecular oxygen. Oxygen captures the free radicals to form stable peroxides and the polymerization thus stops. The continuous influx of oxygen into the coating layer during the irradiation process inhibits the polymerization reaction at the top surface.
The thickness of the inhibited layer is a function of the reactivity of the formulation and function of the rate of irradiation. A high dose rate of radiation helps to reduce the thickness of the non-polymerized layer. Longer irradiation time normally does not help and cannot substitute the need for intense radiation.
The most effective way to eliminate oxygen inhibition is to work in the absence of oxygen. That can be achieved by either working with a cover foil over the fluid. This is typically the situation in a lamination process. In other cases, working with an inert atmosphere is the better solution. Nitrogen is the most frequently used gas. Other inert gases are Argon and carbon dioxide.
Other less frequently used solutions are irradiation under a vacuum or under a layer of water.
Note: Inerting is only necessary at the instant of irradiation. No need for inerting before or after irradiation.
Most equipment manufacturers offer optional inert curing systems which are based on passing the substrate through a chamber under a positive pressure of nitrogen and irradiation through a quartz window.
For smaller lab installations, one can easily build an inert chamber. The following schemes demonstrate a few optional designs plus Do and Do-Not-Do principles.
The general idea is not to use a free flow of nitrogen over the object because that causes a Ventury dragging of air onto the surface. As much as possible, the flow of nitrogen has to be in a semi-closed system. A clear foil can replace the expensive quartz window. The family of FEP or PFA (such as Teflon FEP, and Teflon FPA) are the most suitable since they have a high-temperature resistance and perfect transparency through the whole UV/Vis./Nir IR range. These films can be used with highly intense radiation sources. In the case of lower-intensity sources, a simple polyethylene foil (sandwich bag material) will suffice. It is also perfectly clear through the whole UV and Visible range. Almost any other clear film or sheet will work as well. Some plastics such as PET and polycarbonate are only transparent in the UV-A and visible, and they are also fine since all MY Polymers products are activated by 320-390 nm (UV-A) radiation.
Picture 1: Do and Do-Not-Do in fiber bonding:
Picture 2: Situations that do not need inerting:
Picture 3: A scheme of an inerting tray with a transparent EFP foil being used for curing coated glass plates. The following picture shows the actual device.
Picture 4: A simple inerting tray with a transparent EFP foil being used for curing coated glass plates. The construction materials include wood pieces, metal foil, FEP foil, masking tape, nails, epoxy adhesive (to seal cracks), and plastic tubing. Nitrogen enters from the rear part (green tubing). The tubing serves to pull the tray back and forth on the conveyor belt. Aluminum strips surround and protect the transparent foil from overheating.